The COVID-19 outbreak found humanity almost completely unprepared. And while some countries have dealt with the overwhelming risk effectively, it has become clear that extra care should be taken for nursing staff to reduce risk of exposure.
The increased care of nursing staff has come as a result of good cooperation with technology. During this difficult time, voluntary efforts have flourished for 3D printing and the production of raw material of plastics. In Greece, the company “TED3D”, based in Volos, moved quickly and managed to supply the country’s nursing staff with more than 5,000 face shields, as revealed to The Greek Herald by head researcher, Elias Fritzalas.
“It simply came to our notice then. Thus, the ability of companies such as TED3D to play a key role in helping first-line health care providers has emerged,” head researcher Elias Fritzalas says to The Greek Herald.
“On this occasion, the research team was formed, consisting of us, the Department of Mechanical Engineering of the University of Thessaly with Assistant Professor Georgios Saharidis, the Pulmonary Clinic of the University of Larissa with Professor Konstantinos Goupoupiliou of Gourgouliani and the contribution of Dias Elias Karametou.”
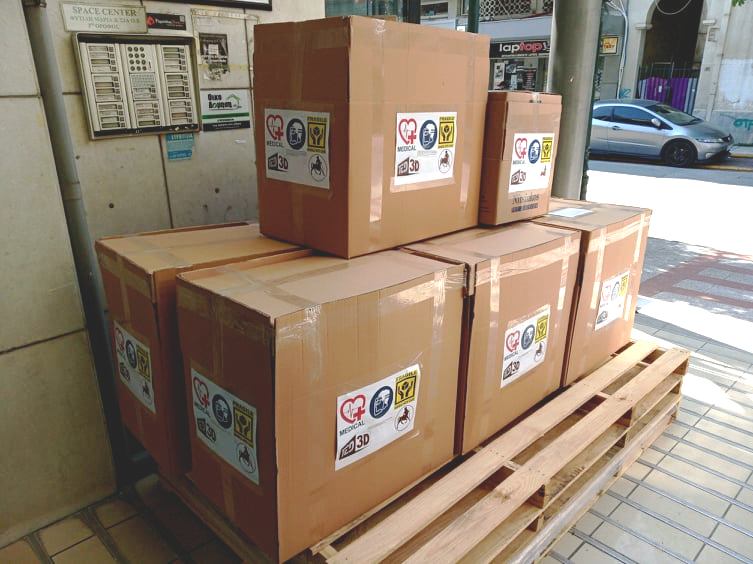
“This group started working about 1 month ago today, recording, studying, designing, producing and testing first-hand items.”
Face shields are used in hospitals across Europe to prevent the direct transmission of coronavirus through bodily discharge. Elias Fritzalas reveals, however, that her face shield is 100% their own design, and possesses important advantages over others.
“It is enclosed, protecting from ear to ear, the whole doll and well below the chin.”
“To date, we have managed to produce and deliver 5000+ face shields and we hope to produce many more.”
3D Printing the “Holy Grail” for mask production
3D Printing has proven to be a saviour device, not only in Greece, but in countries such as Italy and Spain, which have been hit hard by the pandemic.
“In general, the community and the public now tend to consider 3D printing as the “holy grail”, which of course does not apply in all cases,” Mr Fritzalas reveals.

“To give an example, 3D printing, as applied worldwide by the community, has concluded that the shield has a 3D printed frame that takes an average of about 1 hour to produce a mask (the “glass” in front). We, with the plan we have implemented, managed to produce 30 shields per hour…”
The public is advised to stay at home during this epidemic, yet if people are required to engage in public travel, it is recommended that they where a face mask or protection device. While face shields, developed by companies such as TED3D, are only accessible for health care workers, masks and other protective devices are essential to reducing the spread of this global epidemic.